Datasheet LM25149-Q1 (Texas Instruments) - 10
Hersteller | Texas Instruments |
Beschreibung | 42-V Automotive Synchronous Buck DC/DC Controller with Ultra-Low IQ and Integrated Active EMI Filter |
Seiten / Seite | 51 / 10 — LM25149-Q1. www.ti.com. 8 Detailed Description 8.1 Overview. NCE INFO. MA … |
Dateiformat / Größe | PDF / 4.1 Mb |
Dokumentensprache | Englisch |
LM25149-Q1. www.ti.com. 8 Detailed Description 8.1 Overview. NCE INFO. MA TION
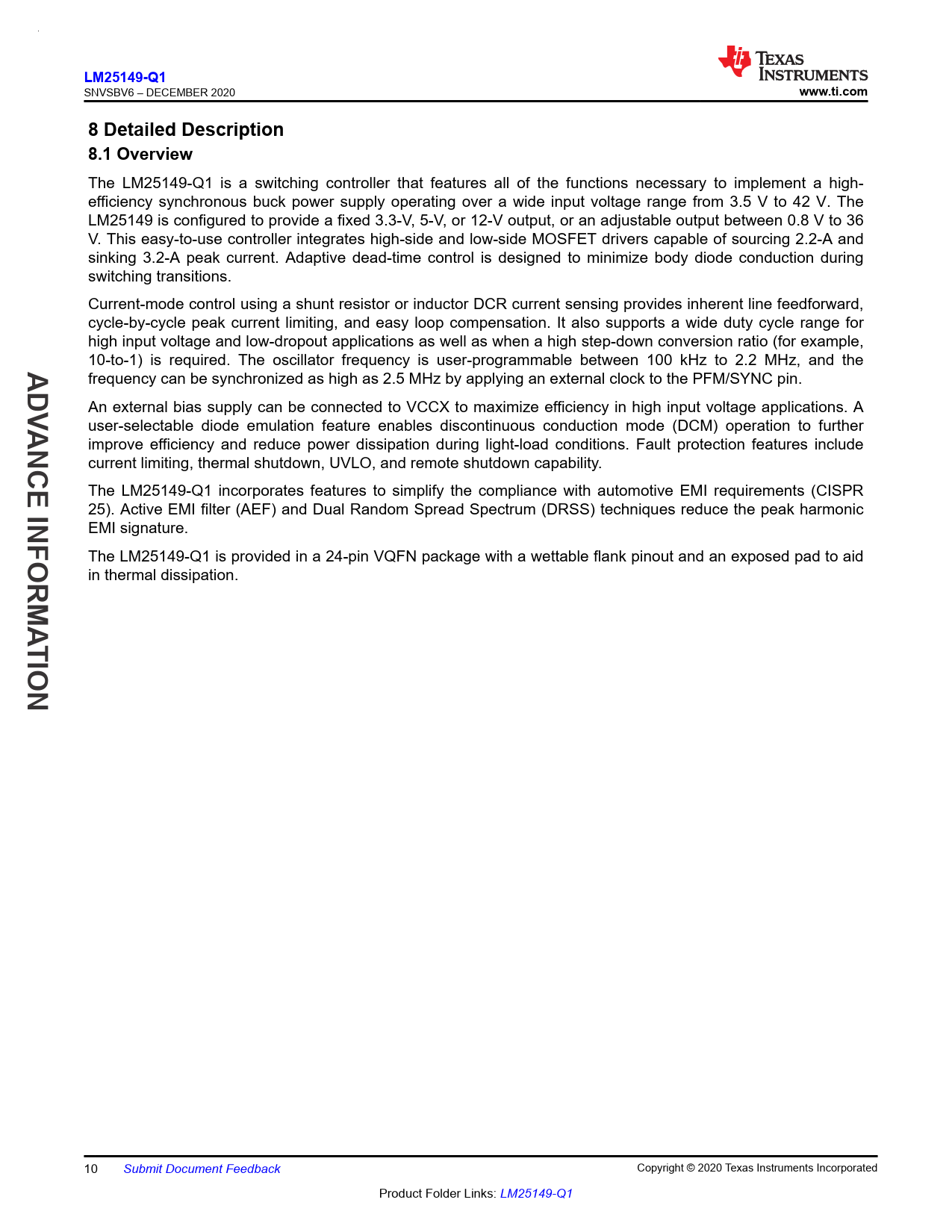
Modelllinie für dieses Datenblatt
Textversion des Dokuments
LM25149-Q1
SNVSBV6 – DECEMBER 2020
www.ti.com 8 Detailed Description 8.1 Overview
The LM25149-Q1 is a switching controller that features all of the functions necessary to implement a high- efficiency synchronous buck power supply operating over a wide input voltage range from 3.5 V to 42 V. The LM25149 is configured to provide a fixed 3.3-V, 5-V, or 12-V output, or an adjustable output between 0.8 V to 36 V. This easy-to-use controller integrates high-side and low-side MOSFET drivers capable of sourcing 2.2-A and sinking 3.2-A peak current. Adaptive dead-time control is designed to minimize body diode conduction during switching transitions. Current-mode control using a shunt resistor or inductor DCR current sensing provides inherent line feedforward, cycle-by-cycle peak current limiting, and easy loop compensation. It also supports a wide duty cycle range for high input voltage and low-dropout applications as well as when a high step-down conversion ratio (for example, 10-to-1) is required. The oscillator frequency is user-programmable between 100 kHz to 2.2 MHz, and the
AD
frequency can be synchronized as high as 2.5 MHz by applying an external clock to the PFM/SYNC pin.
V
An external bias supply can be connected to VCCX to maximize efficiency in high input voltage applications. A
A
user-selectable diode emulation feature enables discontinuous conduction mode (DCM) operation to further
NCE INFO
improve efficiency and reduce power dissipation during light-load conditions. Fault protection features include current limiting, thermal shutdown, UVLO, and remote shutdown capability. The LM25149-Q1 incorporates features to simplify the compliance with automotive EMI requirements (CISPR 25). Active EMI filter (AEF) and Dual Random Spread Spectrum (DRSS) techniques reduce the peak harmonic EMI signature. The LM25149-Q1 is provided in a 24-pin VQFN package with a wettable flank pinout and an exposed pad to aid
R
in thermal dissipation.
MA TION
10 Submit Document Feedback Copyright © 2020 Texas Instruments Incorporated Product Folder Links: LM25149-Q1 Document Outline 1 Features 2 Applications 3 Description Table of Contents 4 Revision History 5 Description (continued) 6 Pin Configuration and Functions 6.1 Wettable Flanks 7 Specifications 7.1 Absolute Maximum Ratings 7.2 ESD Ratings 7.3 Recommended Operating Conditions 7.4 Thermal Information 7.5 Electrical Characteristics 7.6 Active EMI Filter 8 Detailed Description 8.1 Overview 8.2 Functional Block Diagram 8.3 Feature Description 8.3.1 Input Voltage Range (VIN) 8.3.2 High-Voltage Bias Supply Regulator (VCC, VCCX, VDDA) 8.3.3 Enable (EN) 8.3.4 Power Good Monitor (PG) 8.3.5 Switching Frequency (RT) 8.3.6 Active EMI Filter 8.3.7 Dual Random Spread Spectrum (DRSS) 8.3.8 Soft-Start 8.3.9 Output Voltage Setpoint (FB) 8.3.10 Minimum Controllable On-Time 8.3.11 Error Amplifier and PWM Comparator (FB, EXTCOMP) 8.3.12 Slope Compensation 8.3.13 Inductor Current Sense (ISNS+, VOUT) 8.3.13.1 Shunt Current Sensing 8.3.13.2 Inductor DCR Current Sensing 8.3.14 Hiccup Mode Current Limiting 8.3.15 High-Side and Low-Side Gate Drivers (HO, LO) 8.3.16 Output Configurations (CNFG) 8.3.17 Single-Output Two-phase Operation 8.4 Device Functional Modes 8.4.1 Standby Modes 8.4.2 Pulse Frequency Modulation and Synchronization (PFM/SYNC) 8.4.3 Thermal Shutdown 9 Application and Implementation 9.1 Application Information 9.1.1 Power Train Components 9.1.1.1 Buck Inductor 9.1.1.2 Output Capacitors 9.1.1.3 Input Capacitors 9.1.1.4 Power MOSFETs 9.1.1.5 EMI Filter 9.1.2 Error Amplifier and Compensation 9.2 Typical Application 9.2.1 Design Requirements 9.2.2 Detailed Design Procedure 9.2.2.1 Custom Design With WEBENCH® Tools 9.2.2.2 Custom Design With Excel Quickstart Tool 9.2.2.3 Buck Inductor 9.2.2.4 Current-Sense Resistance 9.2.2.5 Output Capacitors 9.2.2.6 Input Capacitors 9.2.2.7 Frequency Set Resistor 9.2.2.8 Feedback Resistors 9.2.2.9 Compensation Components 9.2.2.10 Active EMI Components 9.2.3 Application Curves 10 Power Supply Recommendations 11 Layout 11.1 Layout Guidelines 11.1.1 Power Stage Layout 11.1.2 Gate-Drive Layout 11.1.3 PWM Controller Layout 11.1.4 Active EMI Layout 11.1.5 Thermal Design and Layout 11.1.6 Ground Plane Design 11.2 Layout Example 12 Device and Documentation Support 12.1 Device Support 12.1.1 Development Support 12.1.2 Custom Design With WEBENCH® Tools 12.2 Documentation Support 12.2.1 Related Documentation 12.2.1.1 PCB Layout Resources 12.2.1.2 Thermal Design Resources 12.3 Receiving Notification of Documentation Updates 12.4 Support Resources 12.5 Trademarks 12.6 Electrostatic Discharge Caution 12.7 Glossary 13 Mechanical, Packaging, and Orderable Information